When deciding whether to use the Continuous Cooling Crystallization process to make easily separable Crystals, the challenge is to prove the concept before investing large sums of money in the capital plant. Whether the crystals are to be disposed of (e.g., Cyanide Salts from a plating Bath) or are of high value (specialty chemicals), cooling must provide the crystals. A simple and cost-free method to determine this is done by placing a quantity of the fluid from which the crystals are to be separated into a beaker or similar and placing that into a refrigerator. This way, initial crystal nucleation can be seen, and the temperature at which this occurs is recorded. Ideally, to calculate the size and scope of a Scraped Surface Heat Exchanger (SSHE) needed for scale-up, a solubility curve is needed.
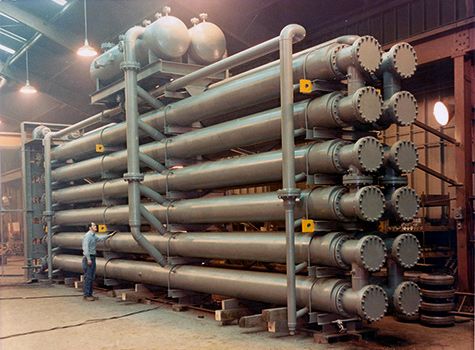
Once cooling has produced crystals, it is usual for the customer to rent a Pilot SSHE and perform trials at the site. A Pilot SSHE provides for the measurement of crystal growth, and it helps in the control of residence time using a recycle loop (usually on a 10:1 ratio that shows morphology and color pick up). Trials require the user to provide utilities such as coolant, pumps and piping, recycle vessels/stirred vessels (as saturation occurs), and downstream separation as the crystals leave as a slurry in solution.
Pilot Scraped Surface Crystallizer
SCRAPED SURFACE HEAT EXCHANGERS
Scale-up is calculated for production runs once the process is proven. SSHE allow for unlimited scale-up, but scaling down is difficult, so a Pilot SSHE is usually offered in 6″ / 8″ /10″ or 12″ inner pipe sizes with Jacket sizes 8″/10″/12″ and 16″ but usually a 6″/8″ Pilot is chosen. These are about 12 feet in overall length with a scraped length of 8 feet. Electric Motors run 380/440V 3~ and may include a Varispeed Drive if needed. Pilot rental is for a minimum of one month, and before delivery, the materials of construction must be chosen. Typically, the inner pipe will be Stainless Steel and the outer Jacket is carbon steel. Blade material must be tested before the Pilot is put into service. Blade samples are submerged in the process fluid for 48 hours at the appropriate temperature. These are measured and weighed before and after immersion to test for growth or shrinkage. The testing will take place without any chemical attrition to the blades to allow for uninterrupted testing.